Role of Oil and Gas Machine Shops in Precision Manufacturing
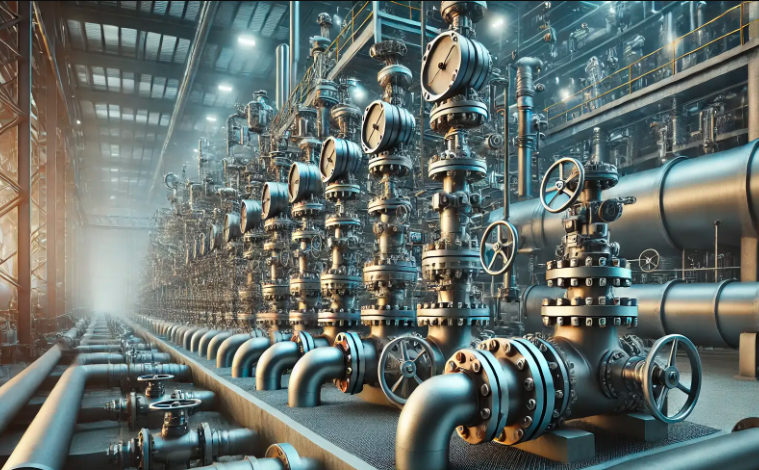
The oil and gas industry relies heavily on high-precision components to maintain efficient and safe operations. From drilling rigs to pipelines, refineries, and offshore platforms, every piece of equipment requires custom machining to ensure durability and performance under extreme conditions. Oil and gas machine shops play a vital role in this process by fabricating, repairing, and maintaining critical components.
In this article, we will explore the importance of machine shops in the oil and gas sector, the machining processes used, key components manufactured, challenges faced, and future advancements shaping the industry.
Importance of Machine Shops in the Oil and Gas Industry
The oil and gas industry operates in some of the harshest environments on the planet, requiring machined parts that can withstand extreme temperatures, high pressures, and corrosive substances. Machine shops specialize in producing high-tolerance components that meet strict industry standards.
1. Custom Fabrication for Unique Requirements
No two oil and gas operations are the same. Machine shops provide customized solutions to manufacture parts that fit specific drilling, refining, and transportation needs.
2. Precision Machining for Critical Components
Precision is essential in oil and gas operations. Machine shops use CNC machining, milling, turning, and grinding to produce components with tight tolerances.
3. Repair and Maintenance of Equipment
In addition to manufacturing new parts Oil and Gas Machine Shopsalso specialize in repairing worn-out components, extending the lifespan of expensive equipment.
4. Reducing Downtime and Costs
Machined components help prevent equipment failures, reducing unplanned downtime and saving millions in repair costs for oil and gas companies.
Machining Processes Used in Oil and Gas Machine Shops
To meet the rigorous demands of the oil and gas industry, machine shops use advanced machining techniques that ensure precision and durability.
1. CNC Machining
Computer Numerical Control (CNC) machining is widely used in oil and gas machine shops. This automated process ensures high precision, repeatability, and efficiency when manufacturing complex components.
2. Turning
Turning is essential for producing cylindrical components like pipes, shafts, and connectors. This process removes material while the workpiece rotates, ensuring accurate dimensions.
3. Milling
Milling is used for shaping flat and contoured surfaces in components such as valve bodies, manifolds, and gear housings.
4. Drilling and Boring
Drilling creates precise holes in metal parts, while boring enlarges existing holes to achieve exact specifications. This is crucial for pipeline fittings, pressure vessels, and pump casings.
5. Grinding and Polishing
Grinding ensures high surface finish and dimensional accuracy for components that require tight tolerances. Polishing enhances corrosion resistance.
6. Welding and Fabrication
Many oil and gas components require fabrication and welding to join metal parts securely. Advanced welding techniques ensure strong and durable connections.
Key Components Manufactured by Oil and Gas Machine Shops
Machine shops produce a wide range of components used in oil and gas exploration, drilling, refining, and distribution.
1. Drill Bits and Downhole Tools
- PDC drill bits for cutting through tough rock formations
- Downhole motors and stabilizers for directional drilling
2. Valves and Fittings
- Gate valves, check valves, and ball valves for flow control
- Pipe fittings, couplings, and adapters for secure connections
3. Pipeline and Wellhead Components
- Flanges, gaskets, and seals for leak-proof joints
- Casing heads and tubing hangers for wellhead integrity
4. Pump and Compressor Parts
- Impellers, casings, and shafts for high-performance pumps
- Compressor blades and rotors for gas processing
5. Offshore and Subsea Equipment
- Blowout preventers (BOPs) for safety in drilling operations
- Riser systems and subsea connectors for offshore drilling
Challenges Faced by Oil and Gas Machine Shops
Despite their crucial role, oil and gas machine shops encounter several challenges that affect production efficiency and profitability.
Read also: CNC Milling Service: Precision Machining for Modern Manufacturing
1. Machining Tough Materials
The industry requires high-strength materials like Inconel, titanium, and hardened steel, which are difficult to machine and cause rapid tool wear.
2. Stringent Industry Regulations
Machine shops must comply with strict standards such as API (American Petroleum Institute), ASME, and ISO, requiring precise documentation and quality control.
3. High Production Costs
Machining high-performance components is expensive due to the cost of materials, labor, and advanced machinery.
4. Supply Chain Disruptions
Global supply chain issues can cause delays in raw materials and machine parts, affecting project timelines.
5. Extreme Environmental Conditions
Oil and gas components must withstand corrosion, high pressures, and extreme temperatures, requiring advanced coatings and treatments.
Future Trends in Oil and Gas Machine Shops
The industry is evolving with technological advancements that improve efficiency, sustainability, and precision.
1. Automation and Robotics
Machine shops are increasingly using robotic automation and AI-driven CNC machines to enhance productivity and accuracy.
2. 3D Printing and Hybrid Manufacturing
Additive manufacturing (3D printing) is being integrated with CNC machining to reduce material waste and accelerate prototyping.
3. Advanced Coating Technologies
New coatings improve resistance to wear, corrosion, and high temperatures, extending component lifespan.
4. Sustainable Machining Practices
Machine shops are adopting eco-friendly processes, such as recycling metal waste and using energy-efficient machining techniques.
5. Predictive Maintenance with IoT
The use of Internet of Things (IoT) sensors in machining equipment enables real-time monitoring, reducing downtime and optimizing efficiency.
Conclusion
Oil and gas machine shops play a critical role in maintaining the efficiency, safety, and productivity of the industry. By utilizing advanced machining techniques, high-performance materials, and cutting-edge technology, these shops produce essential components for exploration, drilling, refining, and distribution.
Despite challenges such as machining tough materials, meeting strict regulations, and managing production costs, the industry is evolving with automation, hybrid manufacturing, and sustainability efforts. These innovations are shaping the future of oil and gas machining, ensuring higher efficiency, reduced costs, and improved environmental impact.